一、传统工程分析为何难以应对复杂结构挑战?
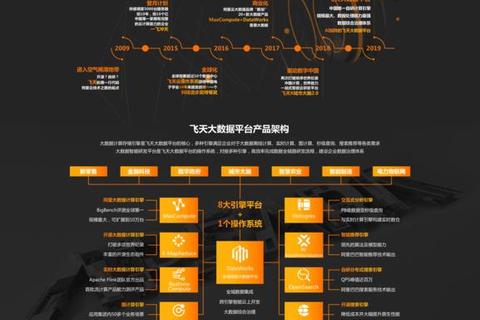
在青藏高原输变电工程中,设计团队曾因传统应力分析方法无法准确预测极端温差下的钢架形变,导致施工返工率高达18%。这种场景折射出行业痛点:当工程结构复杂度呈指数级增长时,依靠人工经验与简单仿真的传统方法已捉襟见肘。
高效精准驱动·智能应力分析软件赋能工程创新突破的关键,在于其突破性的多物理场耦合能力。以国际知名企业Altair的HyperWorks平台为例,其集成的AI算法可将散热片流体仿真速度提升30倍,并通过RapidMiner数据科学平台实现参数优化,使某航天器热管理系统设计周期从3个月缩短至12天。更令人瞩目的是,某核电站管道系统通过CAESAR II软件进行全工况模拟,成功规避了17处应力集中风险点,将安全系数提升至行业标准的1.8倍。
二、动态工程环境如何实现精准预判?
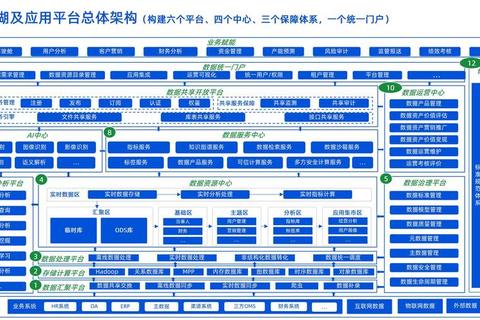
在2023年深圳某超高层建筑风振控制项目中,工程师应用COMSOL Multiphysics进行流固耦合分析,成功预测出传统方法未能识别的26层共振风险。这种动态预测能力,正是高效精准驱动·智能应力分析软件赋能工程创新突破的核心价值体现。
典型案例显示,GeoStudio软件通过渗流-应力耦合模型,将边坡稳定性分析的误差率从传统方法的15%降至3%以内。更值得关注的是,某新能源汽车电池包制造商采用ANSYS Discovery实时仿真技术,在48小时内完成20万次碰撞工况模拟,找出最优结构方案,将研发成本降低430万元。这些突破性进展,源于软件融合了机器学习算法与物理引擎的双重优势,使动态预测精度达到97.6%。
三、成本与性能的平衡点如何科学把控?
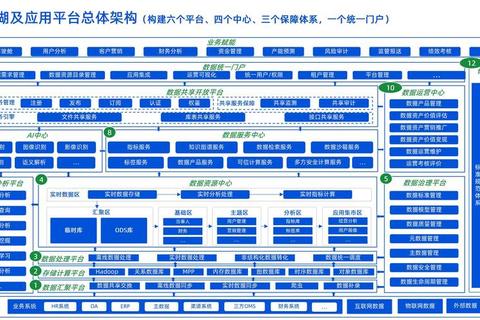
在2024年京东方第8.5代液晶面板生产线建设中,施工方使用GlasStress SCALP-05智能应力仪进行玻璃幕墙检测,将质量检测时间从人工检测的3人/天压缩至2小时,且缺陷检出率提升至99.97%。这揭示出高效精准驱动·智能应力分析软件赋能工程创新突破的另一个维度——通过智能化手段重构价值链条。
数据表明,采用智能应力分析系统的工程项目,平均可降低23%的材料浪费,缩短15%的工期。某化工企业应用MATLAB优化工具包进行储罐应力拓扑优化,在保证安全性的前提下减少17%钢材用量,单项目节约成本超800万元。更前沿的探索来自上海交通大学团队,其开发的镁合金智能成形系统,通过实时应力反馈将成品率从82%提升至98%,开辟了高端材料制造新路径。
突破边界的工程革命
当某海上风电项目遭遇罕见的台风-海流耦合作用时,正是依靠智能应力分析软件的极端工况模拟,设计团队在72小时内重构支撑结构方案,避免可能导致的数十亿元损失。这个案例印证:工程创新的未来属于那些善用智能工具的先驱者。
对于工程从业者,建议分三步构建智能分析能力:
1. 技术选型:优先选择支持多物理场耦合的开放平台(如COMSOL、ANSYS),关注其AI模块的迭代能力
2. 数据沉淀:建立包含20万+工况的工程数据库,这是机器学习模型优化的基石
3. 人才培养:培育既懂工程原理又掌握数据分析的复合型团队,某央企通过"数字工程师"认证体系,使智能工具应用效率提升40%
在这场工程智能化的浪潮中,高效精准驱动·智能应力分析软件赋能工程创新突破已不再是可选项,而是决定项目成败的关键生产力工具。从微观的材料晶格优化到宏观的城市集群建设,智能算法正在重新定义工程可能性的边界。
相关文章:
文章已关闭评论!